- accès direct
Des domaines de compétences au cœur des problématiques
industrielles en matière de transformation numérique.
Science des données
et IA
Interaction et usages
Calcul scientifique
Optimisation
Ingénierie système
Sûreté de fonctionnement
Sécurité numérique et blockchain
IoT et réseaux
– SECTEURS APPLICATIFS
L’expertise de SystemX au service de vos recherches technologiques
Mobilité et transport autonome
Industrie du futur
Défense et sécurité
Environnement et développement durable
- NOS OFFRES
Une proposition de valeur en trois volets
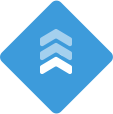
BOOST
Accompagner un industriel pour tester ses solutions technologiques sur un cas d’usage spécifique et en comprendre l’intérêt pour ses lignes de métier.
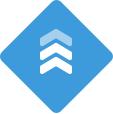
IMPROVE
Consolider des écosystèmes d’innovation avec la conduite de projets R&D collaboratifs afin de lever les verrous scientifiques et technologiques du numérique.
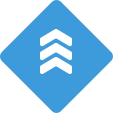
ADVANCE
Fédérer les compétences et l’excellence des académiques autour des défis scientifiques de l’industrie, des services et des territoires.
– L’INSTITUT EN QUELQUES CHIFFRES
L’IRT SystemX c’est …

transferts technologiques

brevets
Et logiciels

partenaires
économiques

publications

plateformes
et équipements

laboratoires
académiques
– EN CE MOMENT
Agenda
Nos dernières actualités
- INSTITUT PORTÉ PAR